Differential pressure, the cornerstone of cleanroom operation, necessitates its precise measurement. Enter the differential pressure gauge, an unsung hero safeguarding controlled environments and facilitating diverse industrial processes.
This article delves into the fundamentals of these crucial instruments, exploring their applications, working principles, and various types of Differential Pressure Gauge.
What is Differential Pressure Gauge
A differential pressure gauge (DP gauge) measures the difference in air pressure between two points within a system. It possesses two ports, aptly named high pressure (HP) and low pressure (LP), for connection to the respective pressure sources.
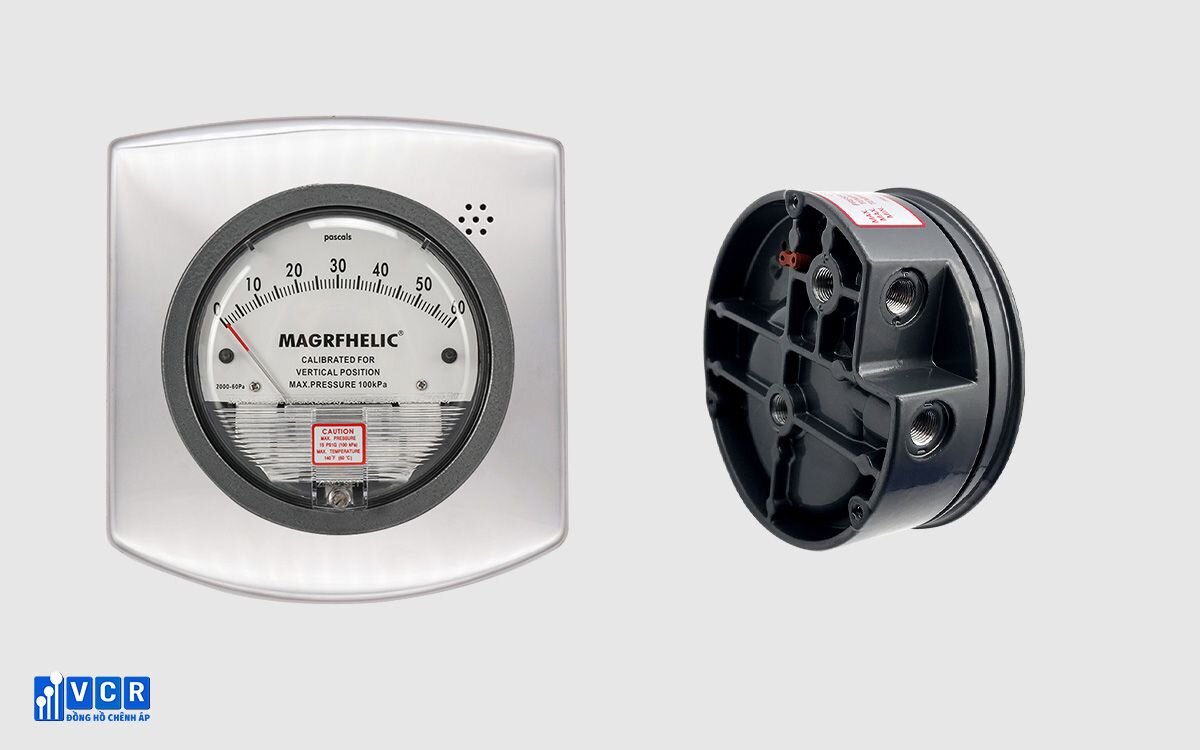
Measurement Units: Measured pressure differentials are commonly expressed in pascals (Pa), kilopascals (kPa), or pounds per square inch (psi).
Reading Interpretation: The gauge displays the pressure difference directly. For instance, if the HP port reads 150 Pa and the LP port reads 100 Pa, the differential pressure is 50 Pa (150 Pa - 100 Pa).
Differential Pressure Gauge: Packed with Features
This differential pressure gauge boasts a versatile range of measuring capabilities:
- Multiple Measuring Ranges: Choose from various options to suit your needs, including 0-60 Pa, -60-60 Pa, 0-250 Pa, 0-500 Pa, and 0-750 Pa.
- Compact and Portable: Weighing only 600 grams per piece, this lightweight gauge is easy to transport and handle.
- Durable Construction: Withstands a maximum pressure of 3 PSI (0.2 bar) and operates in environments ranging from -20°C to +85°C.
- Ingress Protection: The IP65 rating ensures protection against dust and water ingress for reliable operation in various conditions.
- High Accuracy: Delivers precise measurements with an accuracy of ±2.0% FS across most ranges. For the 0-60 Pa range, the accuracy is ±4.0% FS.
- Convenient Connection: Equipped with two pairs of 1/8" ports (high-pressure and low-pressure) on both the left side and back for flexible installation options.
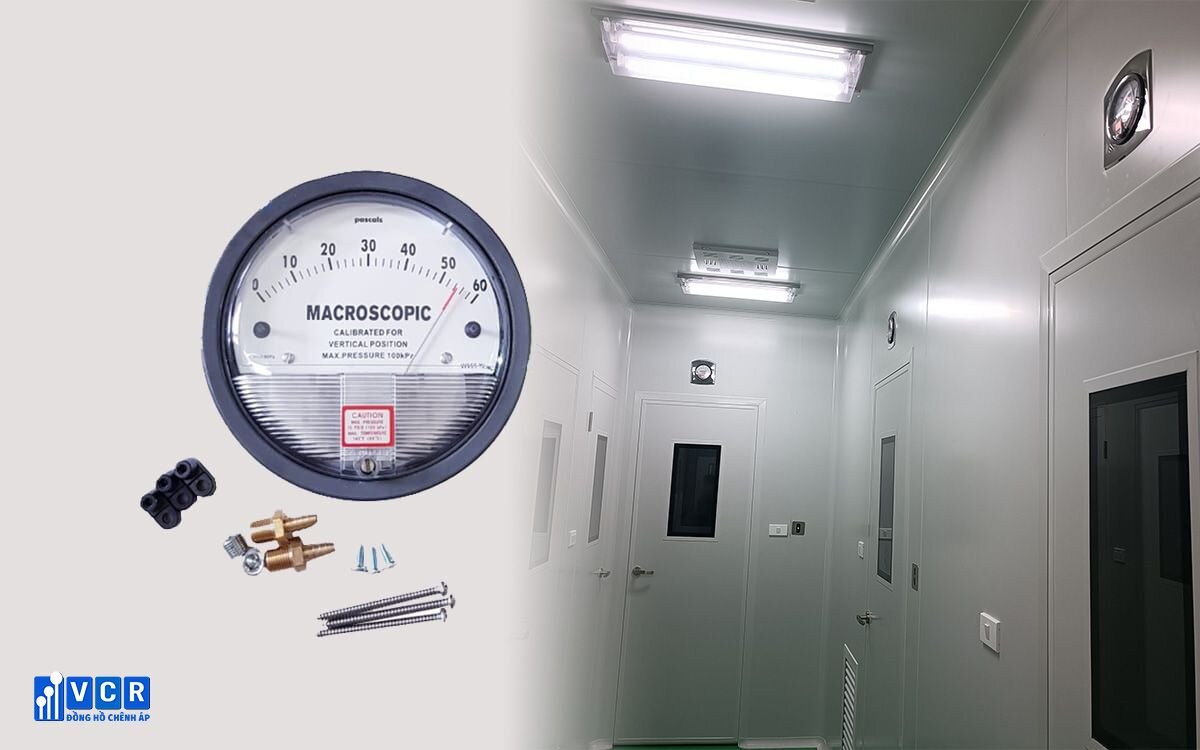
See more: Differential Pressure Gauge in Pharmaceuticals Cleanrooms
Structure of Differential Pressure Gauge
A differential pressure gauge is composed of various essential components meticulously designed for accurate measurement:
- Sensing Element: Serving as the core, it typically consists of a diaphragm or capsule that reacts to pressure differentials between two points.
- Drive Bar: This component, linked to the sensing element, converts pressure-induced motion into rotational movement.
- Magnet: Positioned on the drive bar, it interacts with magnets within the bezel, facilitating pointer rotation.
- Pointer: Prominently displayed on the gauge's face, it provides a visual indication of the pressure differential being measured.
- High-pressure (HP) and Low-pressure (LP) Connections: These ports enable the gauge to connect to corresponding pressure sources within the cleanroom.
- Bezel with Magnets: This fixed ring accommodates permanent magnets that engage with the rotating magnet, thereby governing pointer displacement.
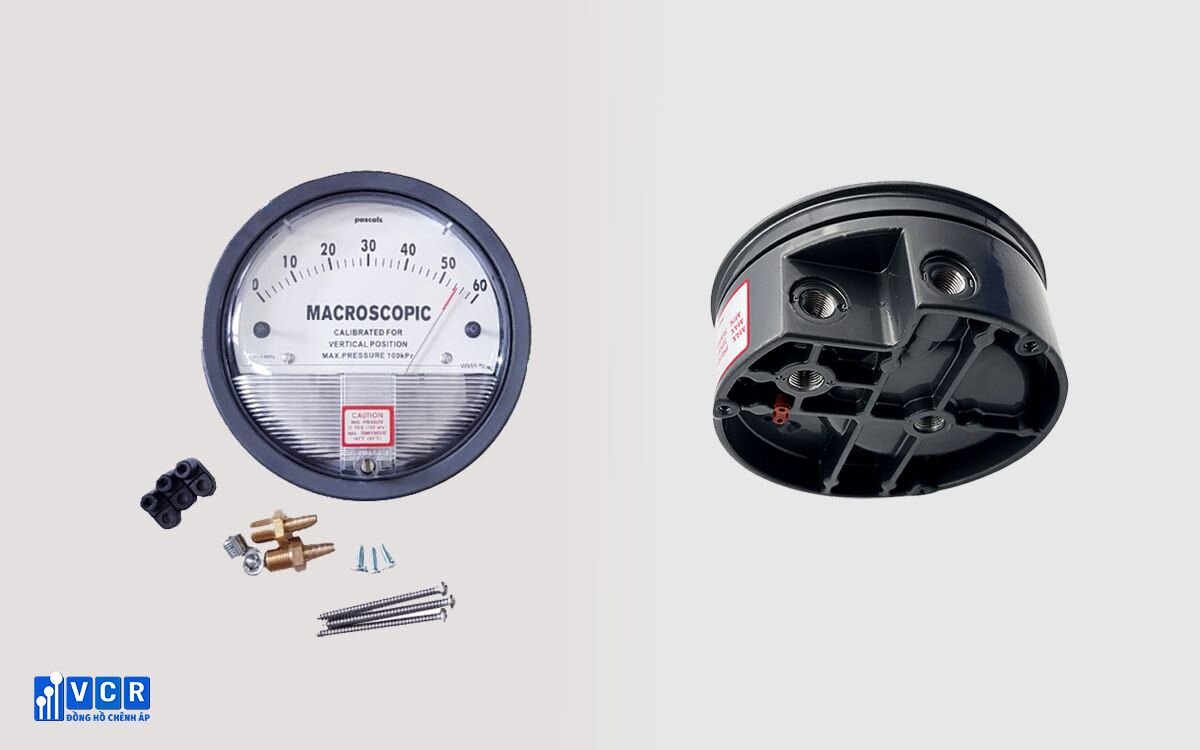
See more: Structure of Differential Pressure Gauge Cleanroom
Beyond Measurement: Unveiling the Working Principles
DP gauges operate on the principle of pressure-induced movement:
- The two ports are connected to the pressure sources.
- The pressure difference causes the diaphragm (a flexible membrane) within the gauge to deflect proportionally.
- This deflection is translated into a rotary motion by a linkage mechanism.
- A magnet attached to the linkage interacts with the bezel magnets, causing the pointer on the gauge face to rotate, indicating the measured pressure difference.
See more: Workings of Differential Pressure Gauges
Types of Differential Pressure Gauges
Sensing Mechanism:
- Piston type: Utilizes a piston moving in a bore against a spring, suitable for liquid applications or systems allowing fluid bypass.
- Diaphragm type (most common in cleanrooms): Employs a flexible diaphragm against a spring, suitable for measuring air, gas, and liquids.
Display Type:
- Mechanical: Traditional gauges with a dial and pointer for pressure indication.
- Digital: Electronic gauges offering digital display, data logging, and potentially additional features.
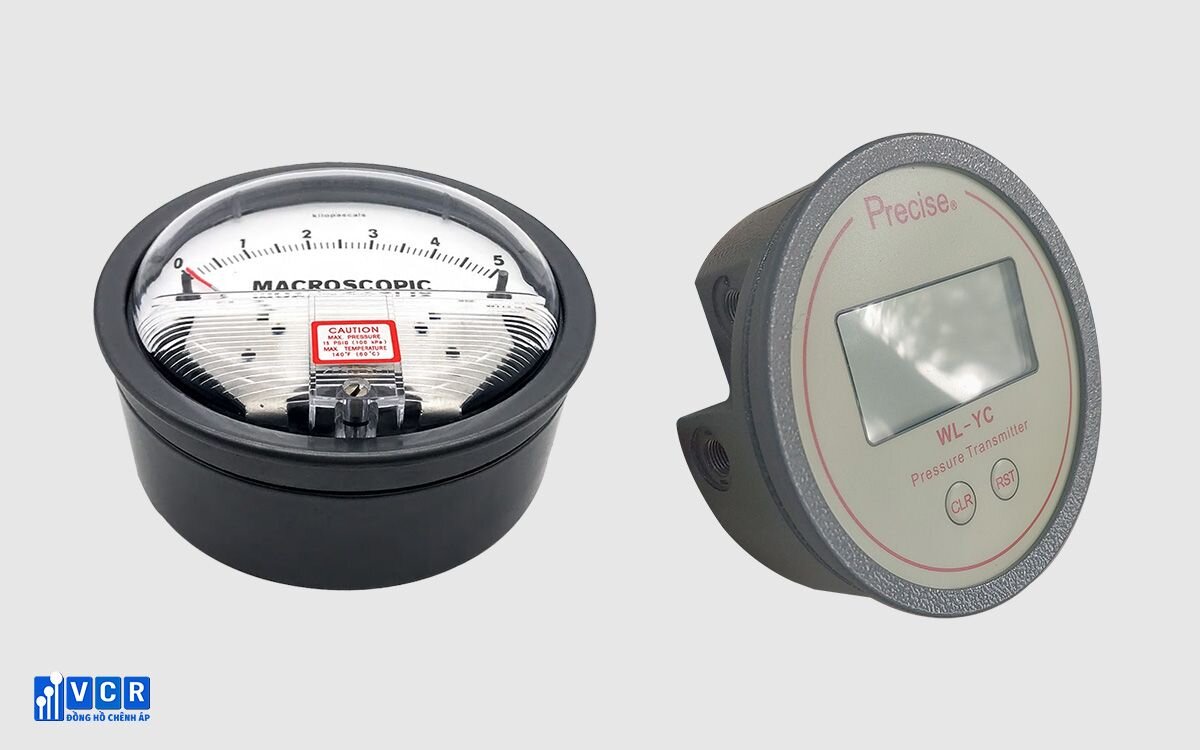
See more: Differential Pressure Gauges for Air Filters
Beyond Cleanrooms: A Spectrum of Applications
DP gauges transcend the realm of cleanrooms, demonstrating their versatility across various industries:
- Measuring Fan and Blower Performance: Assessing the pressure generated by fans and blowers is crucial for optimizing ventilation systems and ensuring proper air circulation.
- Determining Air Velocity: By measuring the pressure differential across a specific orifice placed in an airflow path, DP gauges can determine air velocity, essential for tasks like assessing air quality and optimizing ventilation.
- Calculating Flow Rates: In conjunction with orifice plates, venturi tubes, or pitot tubes, DP gauges enable the calculation of flow rates in pipelines and ducts by measuring the pressure differential across these elements.
- Monitoring Liquid Levels: The pressure difference between the atmosphere and a submerged tube open at the bottom (bubbler system) is proportional to the liquid level in a tank or vessel, allowing DP gauges to monitor liquid levels effectively.
- Ensuring Filter Performance: As a filter becomes clogged, the pressure difference across it increases. DP gauges monitor this pressure difference, enabling timely filter replacement and maintaining optimal performance.
- Fluidic Systems Control: These systems utilize fluids for control and amplification. DP gauges measure pressure variations within these systems, ensuring proper operation.
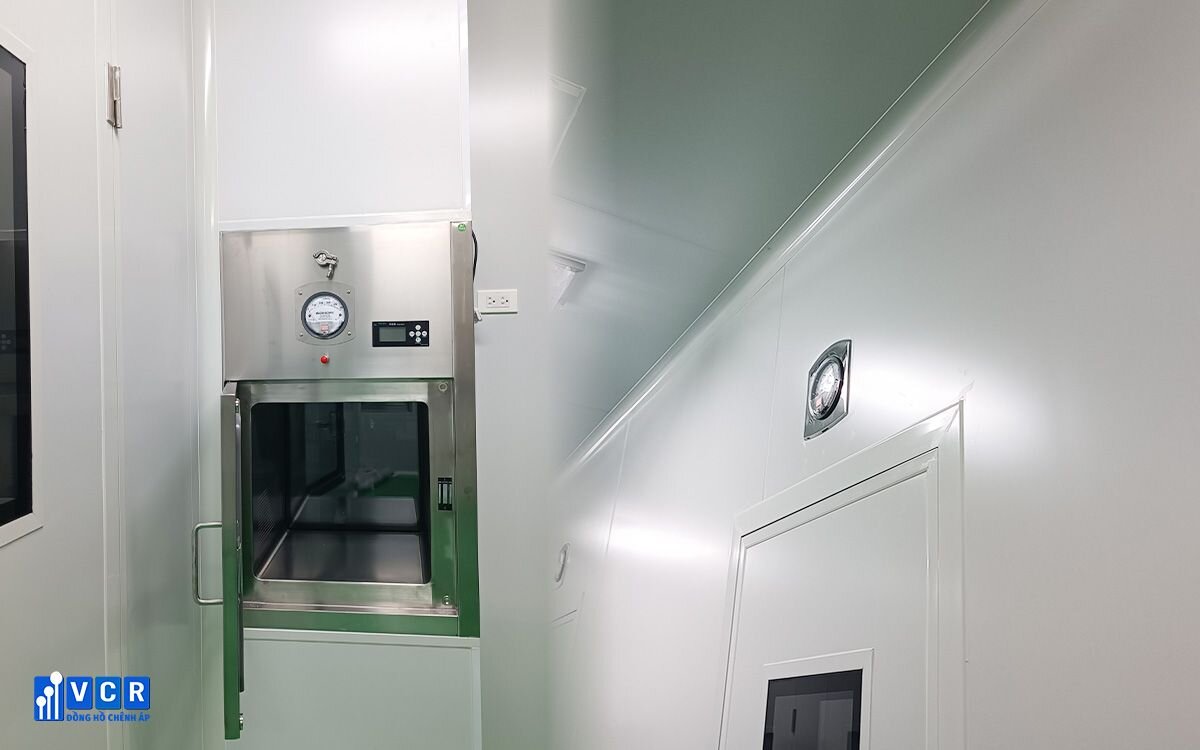
See more: Applications of Differential Pressure Gauges
Widespread Industrial Adoption
The diverse applications of DP gauges translate to their widespread use in numerous industries, including:
- Chemical Processing: Monitoring pressure differentials in reactors, pipelines, and filtration systems.
- Oil Refineries: Measuring pressure drops across filters, valves, and pipelines for optimal operation and safety.
- Gas Liquefaction: Monitoring pressure during the process of converting natural gas into a liquid state.
- Power Plants: Ensuring proper functioning of boilers, turbines, and other equipment by monitoring pressure differentials.
- Pharmaceutical Manufacturing: Maintaining sterile environments by monitoring pressure differentials in cleanrooms and filter systems.
- Food Production: Controlling pressure during various processing steps like mixing, cooking, and packaging.
- General Industrial Processes: Monitoring pressure differentials in a wide range of applications, such as compressed air systems, hydraulic systems, and ventilation systems.
See more:
High Differential Pressure in Cleanrooms
Differential Pressure Gauge Calibration
Differential Pressure Gauge Installation
Conclusion:
Differential pressure gauges are much more than mere measuring instruments. They are vital tools in safeguarding cleanroom integrity, optimizing industrial processes, and ensuring efficient operation across diverse applications. Understanding their functionality, various types, and widespread applications empowers individuals to leverage the power of DP gauges effectively.