Differential pressure, a crucial element in cleanroom environments, plays an even more critical role in pharmaceutical cleanrooms, where maintaining sterility and preventing contamination are paramount.
This article delves into the importance of differential pressure within these specialized spaces.
Understanding Differential Pressure
Differential pressure refers to the difference in air pressure between two points within a system. In pharmaceutical manufacturing, this typically translates to the pressure difference between the production area and surrounding areas. This pressure is measured in pascals (Pa), and a differential pressure gauge is utilized to measure the pressure inside and outside the cleanroom.
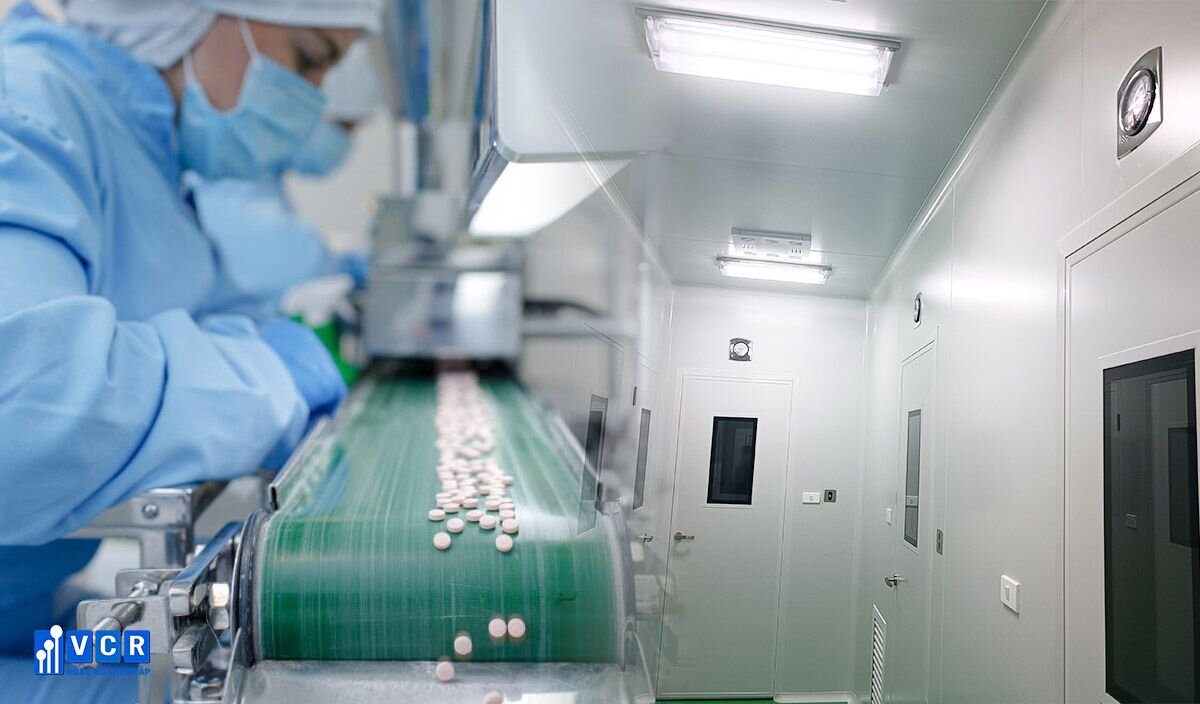
See more: Applications of Differential Pressure Gauges
Maintaining a Positive Pressure Gradient
According to Good Manufacturing Practices (GMP) guidelines established by the World Health Organization (WHO), the widely accepted differential pressure in pharmaceutical cleanrooms is 15 Pa positive compared to surrounding areas. This positive pressure gradient plays a vital role in:
- Preventing Contaminant Ingress: By maintaining higher pressure inside the cleanroom, the flow of air is directed outwards. This acts as a barrier, hindering the entry of dust particles, airborne microorganisms, and other contaminants from adjacent areas.
- Mitigating Cross-Contamination: During processes like granulation, dust particles can be generated, posing a risk of contaminating other products in nearby areas. The positive pressure gradient established by differential pressure helps prevent the spread of these contaminants by directing the airflow outwards.
See more: High Differential Pressure in Cleanrooms
Maintaining the Integrity of the Pressure Gradient
Several strategies are employed to maintain the critical positive pressure gradient within pharmaceutical cleanrooms:
- Airlocks: These enclosed spaces act as transition zones between areas with different pressure levels. Personnel and materials must pass through airlocks, which undergo a pressurization and depressurization sequence to minimize direct airflow between the cleanroom and non-controlled areas.
- Regular Monitoring and Validation: Maintaining consistent differential pressure is essential. Regular monitoring using differential pressure gauges and periodic validation of the entire HVAC (Heating, Ventilation, and Air Conditioning) system are crucial to ensure the integrity of the pressure gradient.
Conclusion:
Differential pressure is not merely a technical detail; it forms the foundation of a safe and controlled environment in pharmaceutical cleanrooms. By understanding its importance and implementing effective strategies to maintain the positive pressure gradient, pharmaceutical manufacturers can safeguard product quality, minimize contamination risks, and ensure adherence to regulatory requirements.