Maintaining precise differential pressure is vital for safeguarding the controlled environment within cleanrooms across various industries, including electronics, pharmaceuticals, and food production. Deviations from the ideal pressure range can compromise sterility and product quality.
This article delves into the causes and solutions for high differential pressure in cleanrooms, empowering personnel to address the issue effectively.
Understanding the Landscape
- Differential Pressure Variations: Each industry possesses specific contamination control requirements, necessitating different differential pressure regulations. These variations factor in the types of pollutants, product properties, and potential risks associated with specific processes.
- Positive vs. Negative Pressure Environments: Cleanrooms can be designed with either positive pressure, where the air pressure inside the space is higher than the surrounding area, or negative pressure, where the reverse is true. The appropriate pressure type depends on the specific application and its contamination control needs.
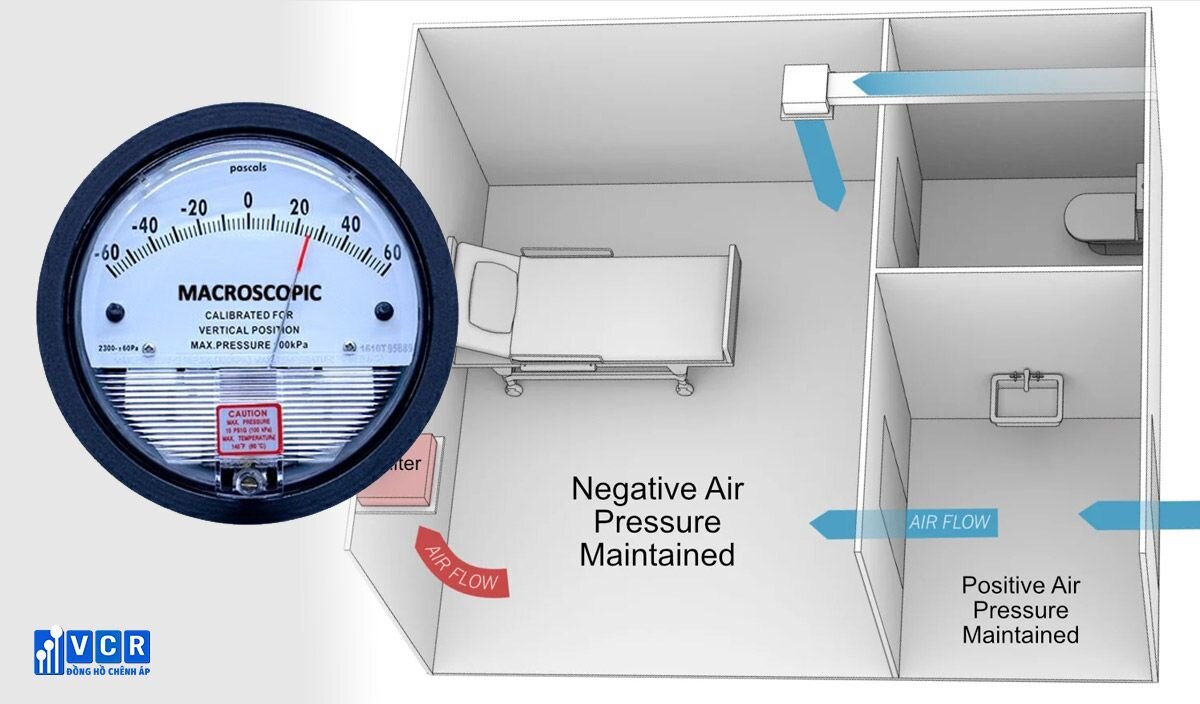
See more: What is A Differential Pressure Gauge
Addressing High Differential Pressure
1. Clogged Filters:
A frequent cause of high differential pressure is excessive resistance within the air filtration system. This often indicates clogged filters that require immediate attention.
Inspection and Replacement: Regularly scheduled inspections and timely replacement of filters are crucial to prevent pressure buildup and ensure optimal filtration performance.
2. Air Handling Unit (AHU) Malfunction:
In some instances, high differential pressure might be attributed to an issue with the differential pressure adjustment system software within the AHU. This scenario necessitates:
Professional Intervention: Engaging qualified technicians to diagnose and repair the AHU software is crucial to restore proper functionality and accurate pressure control.
3. Standard Value Considerations:
Establishing appropriate differential pressure standards is critical.
This process requires thorough consideration of: Product Properties: In pharmaceutical cleanrooms, for instance, understanding the organic chemistry of the drug, processing technology, and potential hazards like allergenicity or harmful byproducts is paramount. This knowledge informs the selection of suitable pressure levels to ensure both product safety and process efficiency.
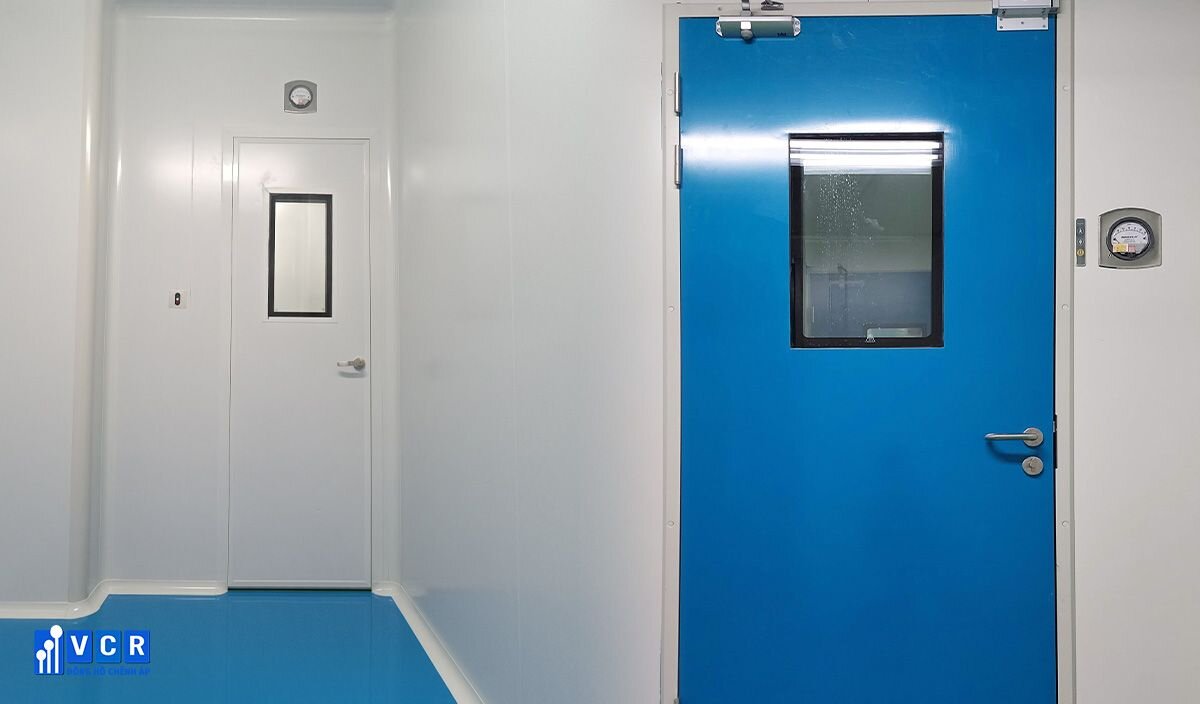
See more: Differential Pressure Gauges in Dispensing Booths
4. Maintaining Pressure Balance:
Cleanrooms necessitate maintaining balanced airflow:
- Positive Pressure Rooms: Employing filtered air supplied through the ceiling creates a positive pressure environment where the internal pressure exceeds the external pressure.
- Negative Pressure Rooms: In contrast, negative pressure rooms maintain an internal pressure lower than the surrounding area by continuously filtering air out of the space.
Conclusion:
High differential pressure in cleanrooms serves as a red flag, prompting immediate investigation and corrective action. By adhering to recommended practices for filter maintenance, engaging qualified personnel for AHU issues, and establishing appropriate pressure standards based on specific needs, cleanroom personnel can effectively address high pressure situations and maintain a safe, controlled environment for optimal product quality and safety.