Differential pressure gauges play a critical role in various industries, including cleanrooms and laboratories, by measuring the pressure difference between two points. To guarantee the reliability and accuracy of these measurements, regular calibration is essential.
This article explains the purpose, procedure, and regulations surrounding differential pressure gauge calibration.
Why We need to Calibrate Differential Pressure Gauge?
Differential pressure gauge calibration serves two primary objectives:
Ensuring Proper Functioning: Calibration verifies that the gauge is operating within its intended specifications and provides accurate readings within its specified range. This helps to:
- Prevent inaccurate measurements: Uncalibrated gauges can provide misleading information, potentially leading to safety hazards and operational issues.
- Maintain consistent performance: Regular calibration helps to identify any deviations from accuracy early on and ensure consistent performance over time.
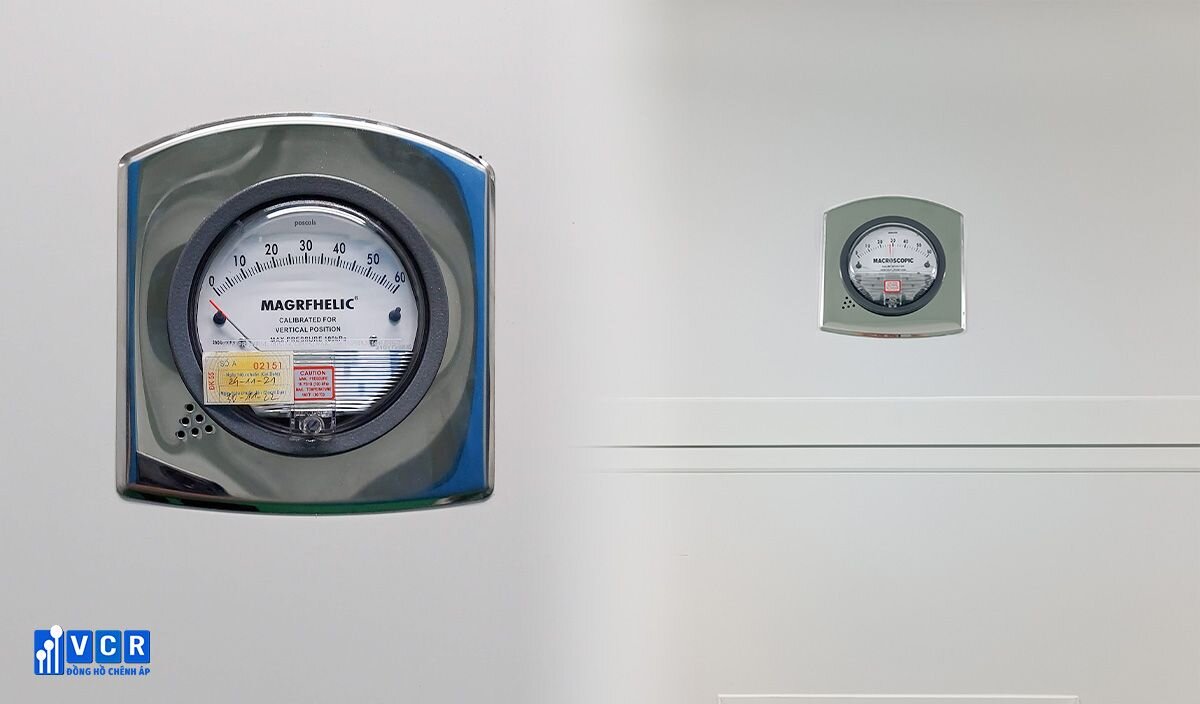
See more: Differential Pressure Gauge Installation
Calibration Procedure
This section outlines a general procedure for calibrating a cleanroom differential pressure gauge . It's important to note that specific procedures may vary depending on the gauge type and manufacturer's recommendations.
Preparation:
- Visual Inspection: Before calibration, check the gauge for any visible damage or functionality issues.
- Data Recording: Prepare a Measurement Data Sheet to record details about the gauge and calibration process.
Calibration Procedure:
- Zero Point Verification: Open both ports of the gauge and expose them to ambient pressure. The needle should rest at the zero position, indicating no pressure difference.
- Pressure Application: Connect the pressure source (e.g., pneumatic pump) to the positive (high) port of the gauge. Leave the low port open to ambient pressure.
- Pressure Generation: Gradually increase the pressure in steps (typically 5 or according to specific requirements) to reach the full scale of the gauge.
- Comparison: At each pressure point, compare the displayed reading on the differential pressure gauge with the reading from a reference standard (e.g., Fluke 754 with pressure module). Record both readings in the data sheet.
- Pressure Decrease: After reaching the full scale, gradually decrease the pressure in the same steps and record the corresponding readings on both the gauge and the reference standard.
- Record Completion: Upon completion, review and document the recorded data and any observations made during the calibration process.
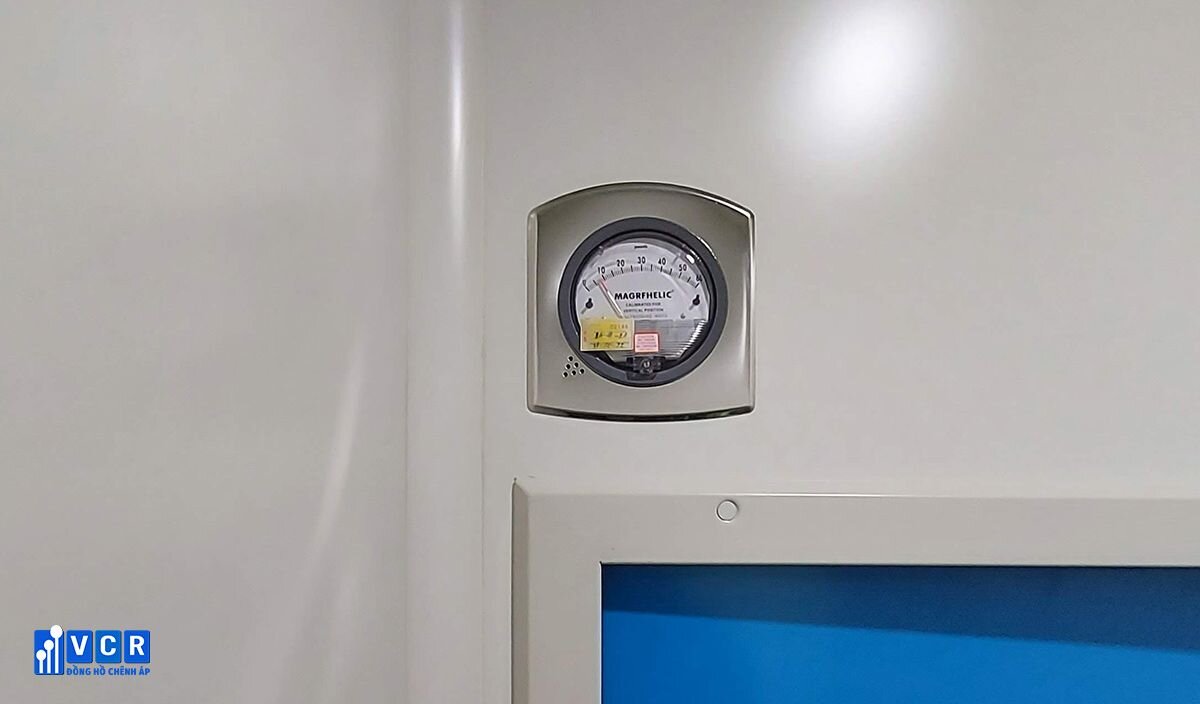
See more: High Differential Pressure in Cleanrooms
Calibration Regulations in Vietnam
In Vietnam, the Law on Occupational Safety and Health mandates that pressure gauges, including differential pressure gauges, comply with specific safety standards. This necessitates calibration by accredited companies and laboratories before their initial use and at regular intervals thereafter.
Conclusion:
Regular calibration of differential pressure gauges is crucial for maintaining accurate measurements and ensuring the safety and efficiency of various operations. By understanding the importance of calibration and adhering to relevant regulations, users can ensure the reliability of their differential pressure gauges and contribute to a safe and productive work environment.