Differential pressure gauges are essential tools in diverse fields, including cleanrooms, laboratories, workshops, dust collection systems, air handling units, and filter monitoring applications. Their ability to accurately measure pressure differences is critical for ensuring proper operation and safety in these settings.
This article delves into the working principle of differential pressure gauges, highlighting the importance of calibration and maintenance.
The Inner Workings
A differential pressure gauge comprises several key components:
- Diaphragm: This flexible membrane separates the two pressure chambers (high and low) within the gauge.
- Magnet: Attached to the diaphragm, this component translates the pressure difference into movement.
- Needle (Pointer): This visually communicates the measured pressure difference on the gauge face.
- Helix: This spiral component acts as a linkage mechanism between the magnet and the needle.
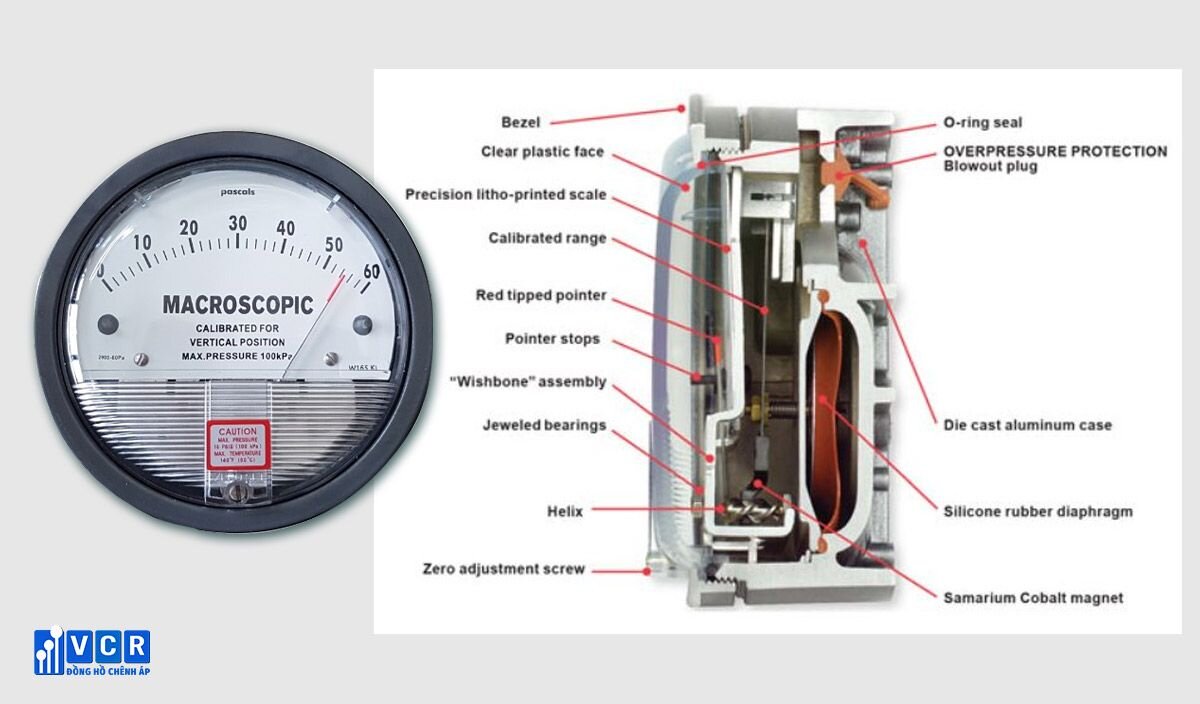
See more: Structure of Differential Pressure Gauge Cleanroom
Operating Principle
- Connection: The higher pressure is connected to the high pressure port, and the lower pressure is connected to the low pressure port.
- Pressure Application: Upon connection, both the high and low pressure chambers fill with their respective pressures, exerting opposing forces on the diaphragm.
- Diaphragm Deflection: The pressure difference causes the diaphragm to deflect proportionally to the magnitude of the difference.
- Magnet Movement: The attached magnet moves in response to the diaphragm's deflection.
- Helix Rotation: The magnet's movement interacts with the helix, causing it to rotate.
- Pointer Movement: The rotating helix translates the movement to the needle, which rotates on the gauge face, indicating the measured pressure difference.
See more: High Differential Pressure in Cleanrooms
Digital Differential Pressure Gauges
In recent times, digital differential pressure gauges have gained popularity. These gauges utilize:
- AC/DC Power Supply: Provides power to operate the gauge.
- Switching Circuit: Converts AC power to DC power for compatibility with the internal electronics.
- Sensor Diaphragm: Similar to the mechanical gauge, it senses the pressure difference.
- Electrical Signal Generation: Based on the sensed pressure, an electrical signal is generated.
- LCD Display: This digital display presents the measured pressure difference in a user-friendly format.
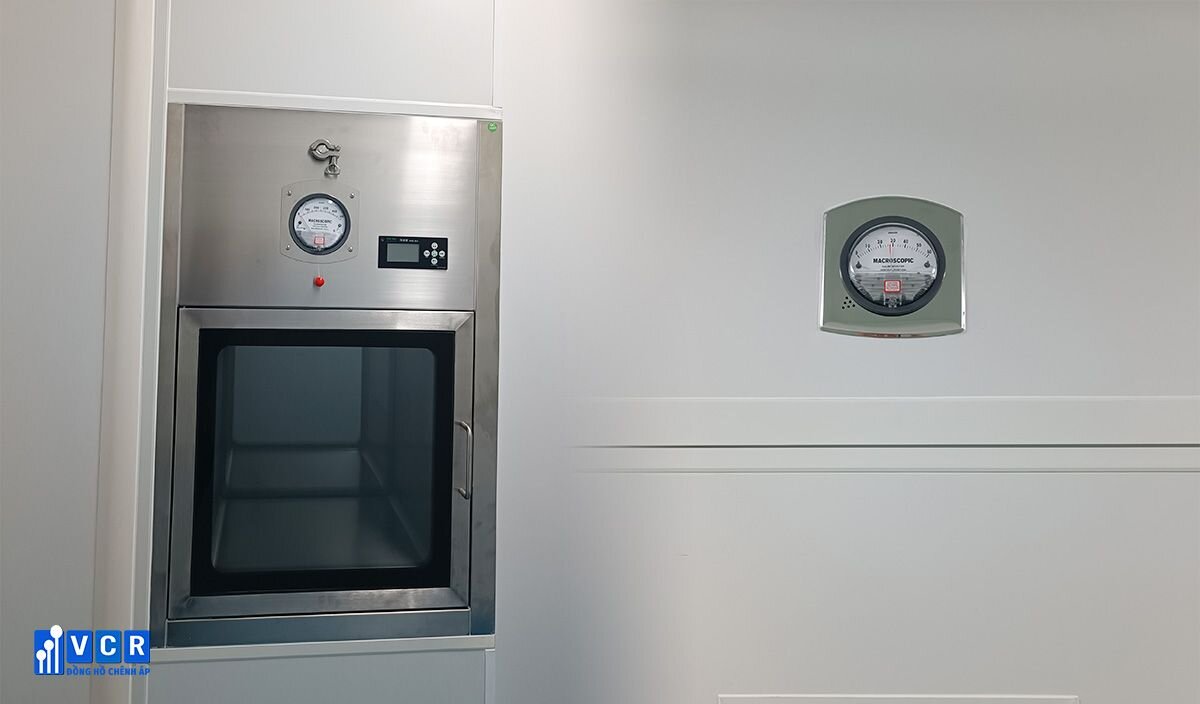
Maintaining Accuracy and Reliability
To ensure accurate and reliable measurements, regular servicing and maintenance of differential pressure gauges are crucial. This includes:
- Calibration: Performed by qualified professionals using specialized equipment, this process ensures the gauge maintains its accuracy over time. Calibration frequency depends on various factors like application, environment, and manufacturer recommendations.
- Importance of Calibration: An uncalibrated or malfunctioning gauge can provide misleading information, potentially leading to safety hazards and operational issues.
See more: Differential Pressure Gauge Costs
Conclusion:
Understanding the working principle of differential pressure gauges and adhering to proper calibration and maintenance procedures are essential for ensuring accurate measurements and optimal performance in various industrial and scientific applications.