The differential pressure gauge (DP gauge) reigns as an unsung hero within the intricate world of cleanrooms.
This specialized instrument transcends the realm of simply measuring pressure; it plays a critical role in safeguarding the controlled environment, ensuring product integrity, and preventing cross-contamination. Let's delve deeper into the diverse applications of DP gauges within cleanrooms:
1. Sentinels of Cleanroom Integrity: Monitoring Pressure Differentials
Strategically mounted atop cleanroom doors, DP gauges act as vigilant sentinels. They continuously monitor the pressure differential between the cleanroom environment (low pressure) and the surrounding area (higher pressure). This crucial function ensures:
- Prevention of cross-contamination: By maintaining a positive pressure inside the cleanroom relative to the outside, DP gauges prevent the infiltration of airborne contaminants that could compromise the sterility of the environment.
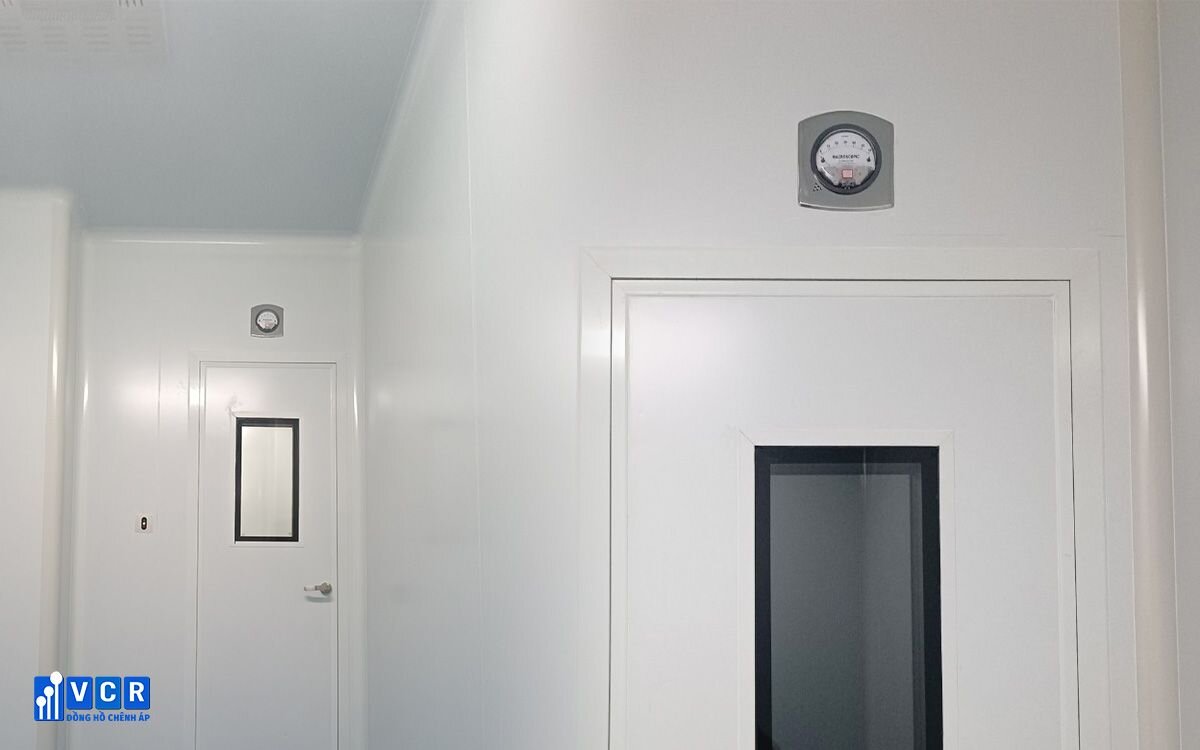
See more: Differential Pressure Gauges in Dispensing Booths
- Maintaining air flow patterns: The pressure differential established by DP gauges guides the directional flow of air within the cleanroom. This controlled air movement is essential for preventing the accumulation of contaminants in specific areas.
- Monitoring pressure variations: DP gauges offer real-time insights into pressure fluctuations within the cleanroom. These deviations can indicate potential issues like leaks in the cleanroom envelope, prompting timely intervention to maintain optimal conditions.
2. Unveiling Liquid Levels: Guardians of Tanks and Vessels
Beyond cleanroom applications, DP gauges extend their reach to various industrial settings. In tanks and vessels, they serve as reliable guardians, measuring the liquid level by harnessing the principle of hydrostatic pressure. Here's how it works:
- A bubbler tube is submerged within the tank, with one end open to the atmosphere.
- As the liquid level rises, the air pressure inside the bubbler tube increases due to the hydrostatic pressure exerted by the liquid column.
- The DP gauge measures the pressure difference between the air pressure in the bubbler tube and the atmospheric pressure, which is directly proportional to the liquid level in the tank.
3. Gatekeepers of the Pass Box: Ensuring Safe Material Transfer
The pass box, also known as a cleanroom transfer hatch, acts as a critical checkpoint for materials entering the cleanroom. Here, DP gauges play a vital role in maintaining the integrity of the cleanroom environment:
- The DP gauge continuously monitors the pressure differential between the interior of the pass box and the cleanroom environment.
- By ensuring that the pressure inside the pass box remains slightly higher than the cleanroom, DP gauges prevent the unfiltered air from the outside environment from entering the cleanroom when the pass box is open.
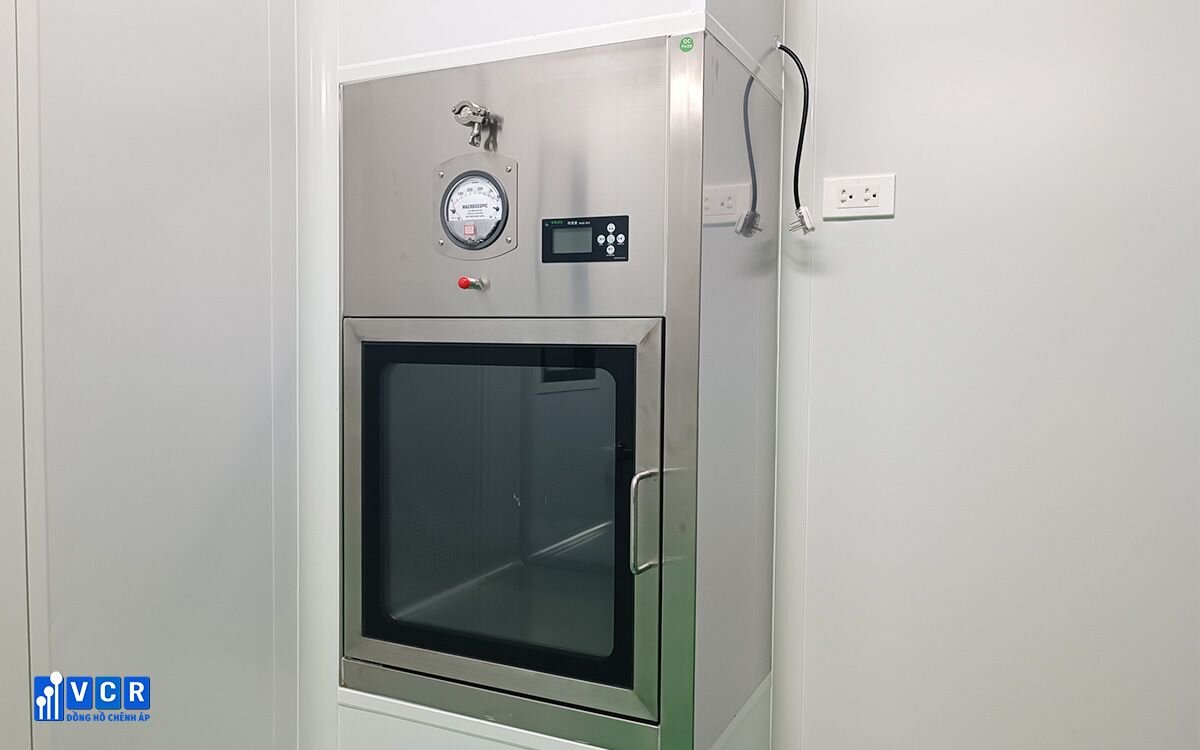
- This pressure barrier safeguards the cleanroom from potential contamination during material transfers, promoting a safe and controlled environment.
4. Filter Integrity: Guardians of Cleanliness in Pharmaceutical Applications
Within the pharmaceutical industry, DP gauges play a crucial role in monitoring the performance of air filters. They measure the pressure difference between the upstream (unfiltered air) and downstream (filtered air) sides of the filter.
An increasing pressure differential across the filter indicates clogging or reduced filter efficiency. This valuable information prompts timely filter replacement, ensuring optimal air quality and safeguarding the sterility of pharmaceutical products.
See more: Differential Pressure Gauge in Pharmaceuticals Cleanrooms
Conclusion:
DP gauges, while seemingly simple instruments, play a multifaceted role in the intricate world of cleanrooms and beyond. From safeguarding controlled environments to monitoring vital processes, these versatile gauges are indispensable tools for ensuring quality, safety, and efficiency in various applications.